National leaders in the foundry
foundry market
With more than 25 years of experience in the market, we are the largest supplier of inputs and raw materials for the foundry and steel industry.
At Quipasur we have designed and patented a molded pellet whose unique shape and formulation allow us to overcome these obstacles and increase system performance.
Historically, foundries have used a number of materials to cover materials to cover the uprights and prevent heat loss in the feeders.
These, however, are not sufficiently efficient as their dosage is operator-dependent and can lead to defects in their dosage depends on the operator and can lead to feed defects due to inadequate defects in the feed due to inadequate application.
In order to overcome these problems, Quipasur has developed its developed its HCP-700 exothermic covering pellet, a cylinder equipped with grooves to ensure grooves that ensure heat transfer by radiation to the inside of the pellet, guaranteeing a rapid the interior of the pellet, guaranteeing a fast reaction of the exothermic exothermic components when they come into contact with the liquid metal.
The exothermic pellet created and patented by Quipasur
It can be applied to all types of ferrous alloys.
It is compatible with exothermic and insulating sleeves. It must be
inserted inside the sleeves before casting.
Ferro
Molybdenum
We manufacture our own product
from molybdenum trioxide and selected raw materials.
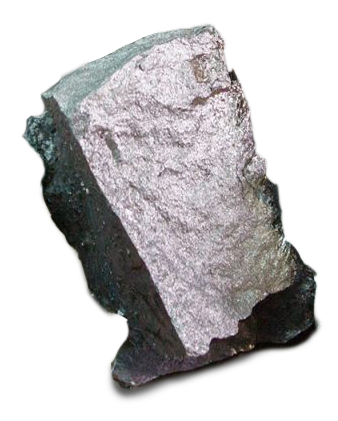
FeMo is produced by an oxidation-reduction reaction, in our reactors, using the aluminothermic principle. reactors, using the aluminothermic principle.
The cake obtained is then cleaned to separate the slag and crushed and crushed mechanically to a previously defined size. defined size.
Characteristic Chemical Analysis
-
Mo60.00% min.
-
C0.12% max.
-
P0.05% max.
-
S0.10% max.
-
Si1.50% max.
Sleeves
Manufacturing
The Exothermic-Insulating Sleeves are manufactured using the following process Urethane Phenolic Cold Box, by means of an automated and automated and meticulously controlled process.
This allows the mixture of components to be homogeneous and of standardized quality, reducing human error considerably.
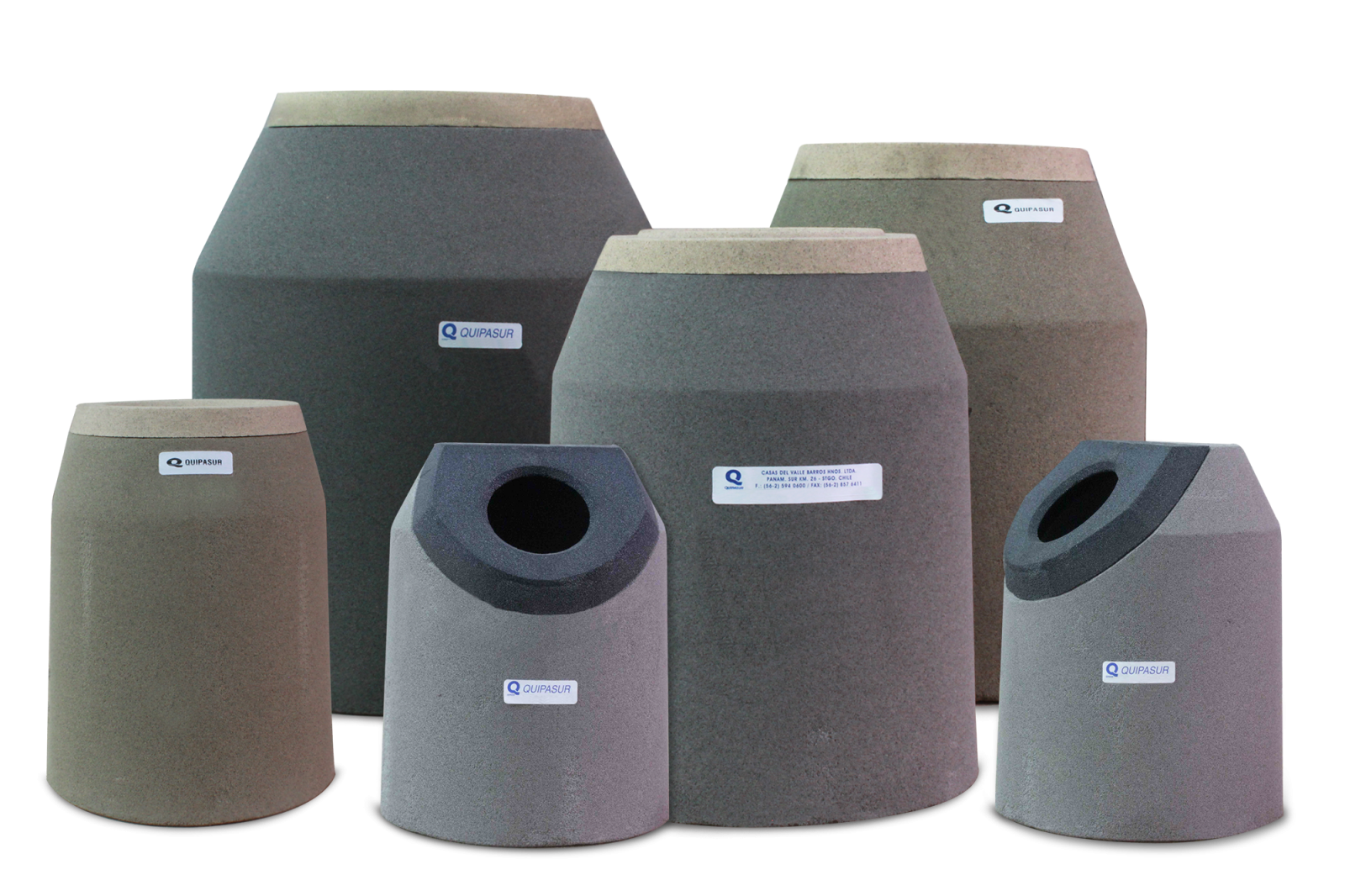
We manufacture a double-layer sleeve, designed for maximum
maximum feed efficiency and made in a two-layer
made in a two-layer cold box process.
The super exothermic inner layer delivers a controlled heat controlled heat input. The highly insulating outer layer allows the exothermic effect in the cooling stage for a longer period of time.
It allows to reduce the nominal diameter of the feeding sleeves, obtaining a obtaining an important metallic saving in all types of alloys.
Less stress is generated in the liquid and solid shrinkage stage.
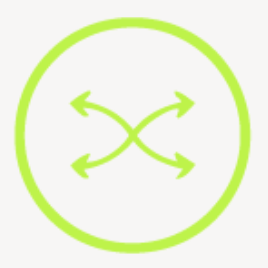
Its use avoids segregation.
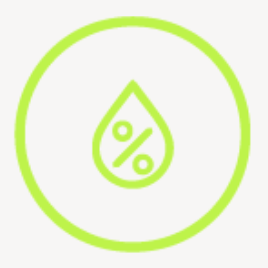
They do not absorb humidity.
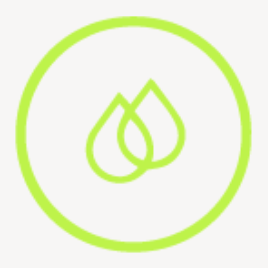
Its quality is homogeneous, avoiding uncertainty due to variable quality.
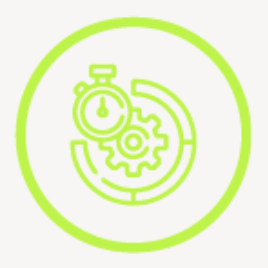
They are more efficient and can be downsized compared to cellulose pulp press sleeves. pressed cellulose pulp sleeves.
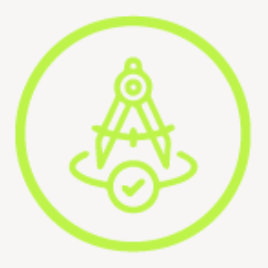
They allow high accuracy, reliability and predictability of simulations.
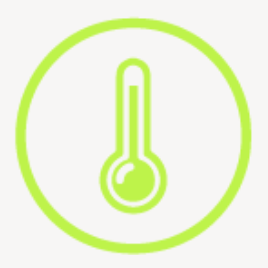
Thermal insulating advantages decrease the effects of sintering of sintering of molding sand.
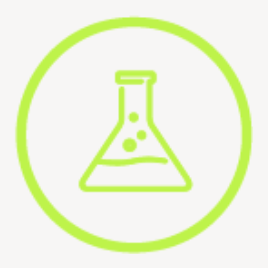
The ignition time and chemical composition is according to the size and/or amount of metal to be contained.
Thermophysical properties are tested by means of simulation software such as: SOLID CAST, MAGMA and others.
Often just considering theoretical values can be far from reality and result in a simulation that is not can be far from reality and result in a suboptimal or erroneous simulation. or wrong simulation. For this reason, we carry out tests, measurements and controls, which allow our clients to optimize their processes, saving time and money.
Efficiency + Predictability + Optimization = SAVINGS
We have a wide variety of sizes and designs.
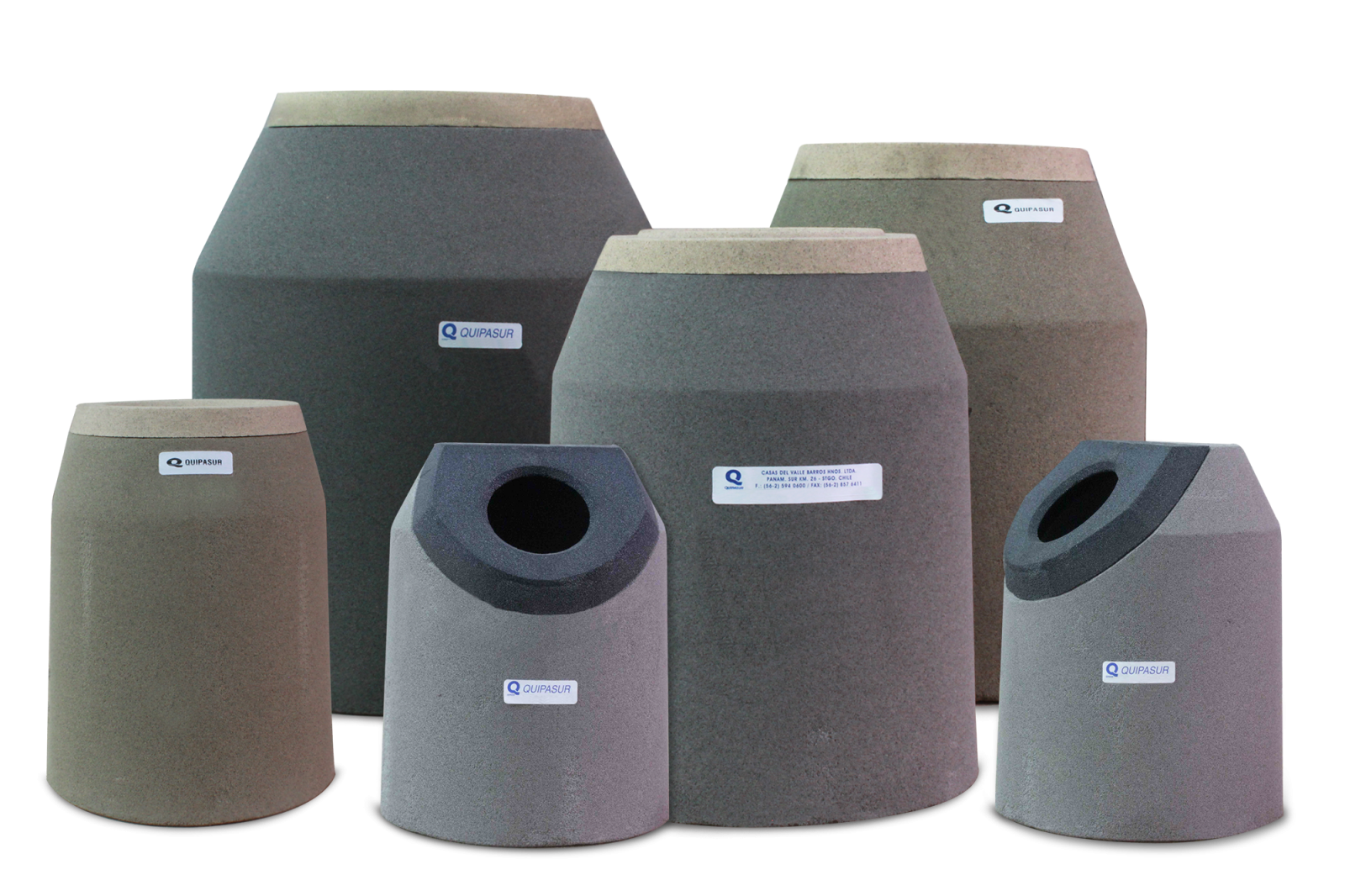
-
Double layer (High efficiency sleeves, capable of lowering up to 4 sizes due to 4 sizes, due to the insulating and exothermic layer)
-
Barrel Sleeves and/or Spherical Sleeves
-
Blind Sleeves.
-
Elbow sleeves, among others.
-
Sizes from 60 mm to 600 mm or more.
Paints
refractory paints
REFRAQUIP 70 FLOW ceramic coating is a highly refractory mold protector of high refractoriness, with its pigment consisting of high purity zirconium oxides.
-
AppearanceOpaque White
-
Density 20°C1,8 - 2,2 grms/cm3
-
Main SolventIso Propanol
-
Density 20°C1,8
The coating is used for the painting of cores and molds made with cold cured resins, either acid or alkaline.
It can be applied by spray, broaching, glue, immersion and blasting.
Resins
FURANIC RESIN FURALQUIP
Furalquip is a resin manufactured by Quipasur in our reactors, under the most reactors, under the most demanding quality standards.
Designed to meet the highest technical and environmental requirements of the acid-catalyzed requirements of the acid-catalyzed furanic autofracturing process, Furalquip's Furalquip resin is characterized by low odor and fume emissions.
ALKALINE PHENOLIC RESIN
Resin for Alkaline Phenolic Alkali self-curing molding process ester catalyzed.
It has a dark reddish appearance and is nitrogen-free. RFQ resins are characterized characterized by a high resistance in the mold, achieving excellent results in castings.
RFQ resin is used in the manufacture of molds and sand cores, ferrous and non-ferrous castings.
Sand for
foundry
From different parts of the world we bring special sands of high quality and high performance quality and performance, for the manufacture of molds and sand cores, keeping a permanent stock in our warehouses.